10 Common Mistakes to Avoid When Implementing WMS and How to Address Them
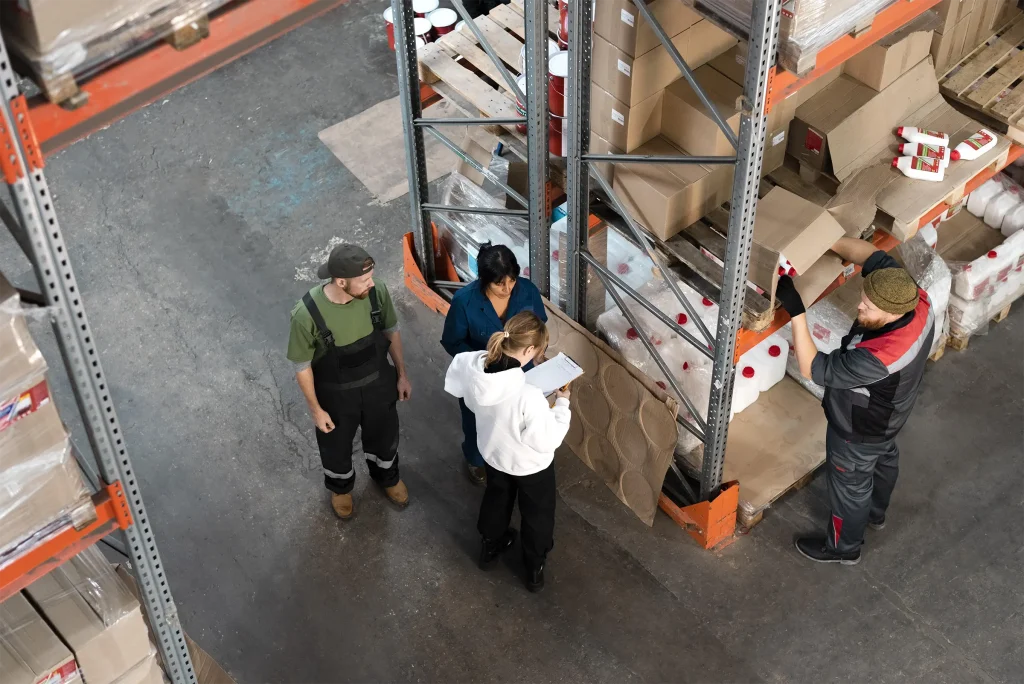
Warehouse Management System (WMS) is a strategic solution for logistics and supply chain or warehouse business owners who are looking for cost and time-effective solutions to streamline their crucial business operations. From optimizing warehouse operations to increased efficiency and improved accuracy, a correctly implemented WMS can bring you a myriad of benefits.
However, the implementation of a warehouse managing system can be complex and fraught with potential pitfalls. Understanding and addressing these common pitfalls is paramount to ensure seamless implementation, eliminate expensive errors, and ensure maximum working efficiency of the new system.
Here are 10 common pitfalls businesses often make when implementing a WMS and proven strategies to address them smoothly and swiftly.
Mistake 1: Inadequate Planning
Impact: Rushing into a WMS implementation without thorough planning and assessing the business needs or requirements can lead to significant issues, financial losses, and even ruining the whole investment.
Solution: Conducting a comprehensive needs assessment to understand your business needs or requirements and the creation of a detailed project plan is the best way to address such issues. Make sure the plan must include timelines, resource allocation, and risk management strategies.
Mistake 2:Overlooking Vendor Reliability
Impact: Choosing a WMS vendor based solely on cost or superficial features and overlooking their credibility, track record, and market reputation can result in making wrong choices, financial scams, and poor quality services.
Solution: thoroughly search and shortlist potential vendors and then compare their credibility, pricing plans, track record, and other features to make the final decision.
Mistake 3:Insufficient Training
Impact: It usually results in poor system handling, frequent errors, and employee dissatisfaction.
Solution: Before implementing a WMS, make sure to create a comprehensive training program that covers all aspects of the WMS and also provides hands-on training sessions to address crucial features or updates.
Mistake 4: Overlooking Data Quality
Impact: Implementing a WMS with inaccurate or incomplete data can lead to operational inefficiencies and errors.
Solution: Conduct a thorough data cleansing and validation process before implementation. Establish data governance practices to maintain data accuracy and integrity. Regularly review and update data to ensure its reliability.
Mistake 5: Lack of Customization
Impact: Assuming a one-size-fits-all approach and failing to customize the WMS to fit specific business needs.
Solution: Work closely with your vendor to tailor the WMS to your unique requirements. Customize workflows, reporting, and user interfaces to align with your operational processes. Ensure the system can scale and adapt as your business grows.
Mistake 6: Ignoring Integration Needs
Impact: Failing to consider how the WMS will integrate with existing systems such as ERP, TMS, and other supply chain software.
Solution: Plan for seamless integration from the outset. Choose a WMS that offers robust integration capabilities. Collaborate with IT and system vendors to ensure data flows smoothly between systems and that integrations are thoroughly tested before going live.
Mistake 7: Underestimating Change Management
Impact: Not preparing the organization for the upcoming changes can adversely impact the work quality and lead to heavy time consumption, unnecessary delays, and a declined reputation in the market
Solution: The only solution to fix this issue is developing a change management plan that includes communication strategies, training, and support.
Mistake 8: Neglecting User Feedback
Impact: Overlooking employee feedback can lead to frustration among the workforce, system incompatibility, and irreparable damages.
Solution: Conducting pilot tests and gathering feedback to make necessary adjustments can help you ensure the system is compatible with your warehouse needs.
Mistake 9: Ignoring Scalability
Impact: Implementing a WMS that meets current needs but cannot scale with business growth.
Solution: Always choose a reliable WMS that can not only align with the current needs but also accommodate future expansion and increased complexity.
Mistake 10: Failing to Measure Success
Impact: It can lead to frequent errors, poor work quality, and system incompatibility with the expanding needs of your business.
Solution: Make sure to establish clear KPIs that align with your business goals, track metrics such as order accuracy, inventory turnover, and labor productivity, and regularly review these metrics to assess the WMS’s performance.
Key Takeaway
Investing in a Warehouse Management System is a strategic decision to transform your warehouse operations, but it requires careful planning, execution, and ongoing management. Its implementation is a bit complicated and carries various risk factors but understanding and avoiding these common mistakes and practicing the above-mentioned, expert strategies can help you ensure seamless and successful implementation.