All About Hydrostatic Test Pump
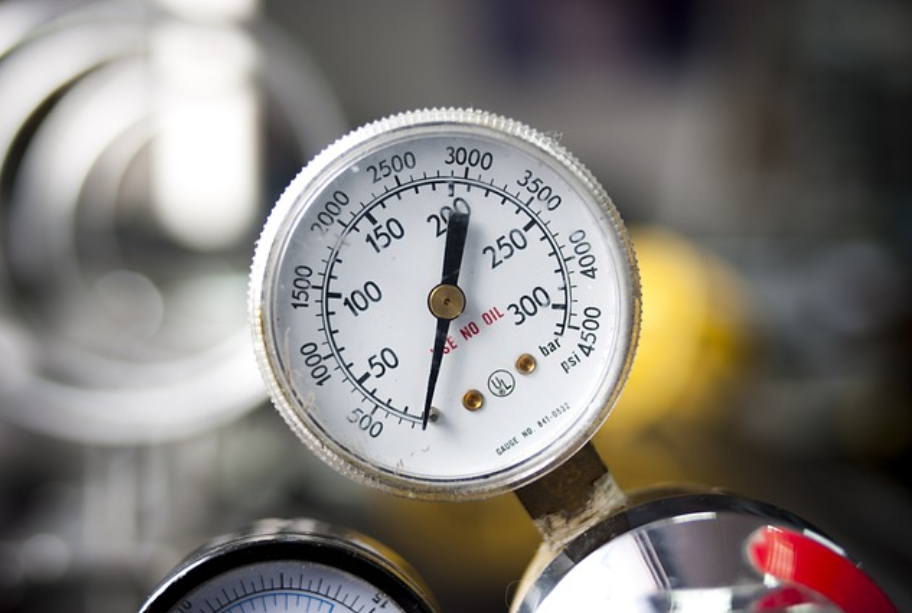
In industries ranging from construction to plumbing, ensuring the integrity of pressure systems is paramount. Hydrostatic testing serves as a vital method to assess the strength and leak-tightness of equipment, helping to identify possibility issues before they escalate into serious problems.
Whether you’re a contractor, engineer, or facility manager, understanding hydrostatic test pumps is essential for maintaining safety and compliance. In this article, we’ll explore what hydrostatic testing is, the types of hydrostatic testing near me, the benefits of conducting regular tests, and critical factors to consider when selecting the right pump for your needs.
What is Hydrostatic Testing?
Hydrostatic testing involves:
- Filling a system with liquid.
- Probably water.
- Testing the pressure to see if it works against the normal operation.
It helps identify weaknesses or defects in material that cause failure. Its use areas include plumbing, oil and gas, construction, and manufacturing, all of which must conform to safety standards and regulations.
Types of Hydrostatic Test Pumps
Hydrostatic test pumps play a very important role in hydrostatic testing. This means that there are several types of hydrostatic test pumps, which vary according to their needs and specifications.
- Hand-operated hydrostatic test pumps
Use manual action, but commonly through a hand crank. Suitable for small applications and mobile, hence ideal for far-flung locations from the test location. It is not suitable for large systems since it is labor-intensive to maintain constant pressure levels.
- Electric Hydrostatic Test Pumps
These are driven electrically, hence easily producing high pressure. They are applied to larger systems and operations that require maintaining a considerable amount of pressure over a relatively longer period of time. The electric test pumps come in various capacities, making them more versatile for different applications.
- Air-Driven Hydrostatic Test Pumps
These are air-driven hydrostatic test pump that run on compressed air and generate large amounts of pressure at much reduced chances of overheating, and thus, they should be employed for a long period. These pumps are extensively used in industries where electricity supply is not efficiently available.
Benefits of Hydrostatic Testing
Some benefits that pressure systems are ascribed for undergoing hydrostatic testing near me make the latter more commonly used. Some of the most important advantages include the following.
- Safety Assurance: One benefit of conducting regular hydrostatic testing is ensuring that systems are safe to operate. Identifying leaks and weaknesses in systems reduces the risks that could lead to catastrophic failure and endanger lives and property.
- Regulatory Compliance: Most industries have been under keen scrutiny for having safe equipment. Hydrostatic testing ensures any enterprise is in full compliance with all regulatory requirements; therefore, no lawsuits or fines would result.
- Cost Effectiveness: Issues detected early through hydrostatic tests save companies considerable costs compared to the repair costs that may be incurred, downtime, and even accidents. Preventive measures prove cost-effective compared to reactive measures.
- Increased Equipment Lifespan: Testing preserves the pressure system’s integrity and prolongs its running. As a result, the equipment stays longer, and reliability increases.
- Quality Assurance: Hydrostatic testing is a part of quality assurance, and manufacturers have to perform it if their products have to be released to the market in accordance with the standard requirements.
Factors to Consider While Choosing the Right Hydrostatic Test Pump
These factors need to be kept in mind in the selection of the appropriate hydrostatic test pump:
Pressure Requirements: Determine the maximum pressure your process requires. The pump’s capability to supply maximum pressure will vary, so it is important to consider this when making your selection.
Mobility: Your tests may need to be performed at several locations. A mobile pump may be your best option. Smaller, lighter units save time and labor with in-the-field operation.
Power Source: Decide between manual, electrical, or air-driven pumps based on what power sources you can and will have available at your test locations. Electric pumps are fast and efficient, but a manual or air-driven pump may be more practical for use at remote test locations.
Capacity: Determine how much fluid you want to test. Larger systems may need a pump that provides higher flow rates in order to fill and accelerate pressure quickly.
Budget: Hydrostatic test pumps vary in price range. Determine a budget and choose the pumps that would give the best value with regard to quality as well as functionality.
Reputation of Manufacturers: Evaluate the best manufacturers and brands. Best-known brands shall provide quality pumps with warranty and better customer service to guarantee reliability.
Conclusion
Hydrostatic testing is an important practice ensuring pressure systems’ safety and integrity in many industrial applications. Being knowledgeable of what hydrostatic testing is and what types of hydrostatic test pumps are available will allow you to make better choices for your testing needs. Be sure to consider things like pressure requirements, portability, and budget when you make your selection.
Wanting “hydrostatic testing near me? “You would wish to choose a good provider who has quality hydrostatic test pumps for that perfect and safe testing. Worth the cost: proper testing equipment and services really mean more than strict compliance on safety, asset protection, and efficient operation as well.